Machine and plant builders reorganize service processes
At the WALDNER Holding GmbH & Co.KG group located in the Allgäu region, an internationally oriented manufacturer of laboratory equipment and systems for the food, pharmaceutical and chemical industry, reliability, efficiency and quality of service are essential pillars for continuous success in the more than 100-year history of the company , In 2014, the company introduced the EcholoN service management software as a central service platform in order to consolidate the heterogeneous system landscape in the IT service management and maintenance service areas and to support the processes with professional tools. Since then, the company has benefited from greater process transparency, cross-departmental standardized service processes, comprehensive evaluations and, last but not least, better service quality in IT support and maintenance.
The WALDNER group of companies with its two legally independent operating companies Hermann WALDNER GmbH & Co. KG and WALDNER Laboreinrichtungen GmbH & Co. KG, with 1,100 employees, is one of the leading specialists for laboratory/school equipment as well as machines and plants for the process industry (food, pharmaceuticals and chemicals). The product range extends from state-of-the-art DOSOMAT filling and packaging systems to fruit cooking systems, water technology and container/plant construction to furnishing systems for laboratories and science classrooms. With its own subsidiaries in France, Great Britain, Italy, Spain, the Netherlands, Switzerland, India, Dubai (UAE), Russia and the United States, the WALDNER Group generated a worldwide turnover of over 190 million euros in 2012/2013.
Consolidation of the different service systems necessary
Until 2012, different island systems were used in IT support and in the maintenance of the company's own machinery. For historical reasons, for example, a software development and change management system was used to support the ERP software used and a singular incident and asset management solution with separate system worlds to support the IT infrastructure. Again, these systems were not suitable for the area of maintenance, so that the service employees had to rely on in-house developed solutions for mapping the maintenance processes.
"Due to the lack of system integration, the bottom line was that process transparency, efficiency and, last but not least, comprehensive functionalities", says Armin Steck, IT manager at WALDNER, describing the situation.
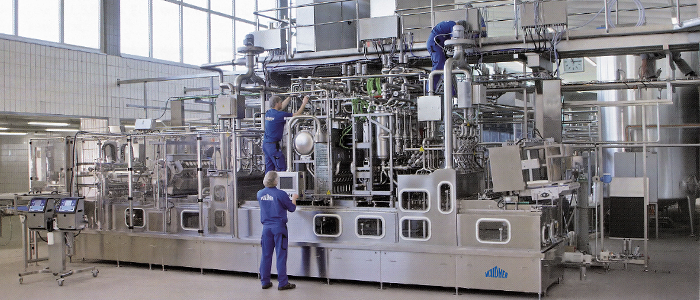
The mechanical and plant engineering company Waldner reorganized the complete service processes in the course of the introduction of the new software. Image: Waldner
"Although we are dealing with largely standardized processes in service - whether in terms of the maintenance of our assets, ERP software or IT infrastructure - the service processes could not be effectively and centrally mapped with our previous IT landscape , We therefore decided in 2013 to consolidate our system landscape in this area and to reorganize the service processes on the basis of a new, uniform service platform. In the medium term, this should also enable WALDNER to connect other service units to the system and use synergies. ”
Open, process-oriented out-of-the-box system required
For the subsequent selection process, WALDNER first summarized the essential requirements at process level, technological level and conceptual level in a catalog of requirements and provided them with an evaluation key. For example, the new system should be very open, flexibly adaptable and process-oriented, so that the requirements in all service areas of the company can be mapped centrally with a uniform platform - regardless of whether the service use involves glued induction switches or a burst pneumatic one Hose, regular maintenance work or troubleshooting when using IT.
With regard to future viability, a modern basic architecture with open interfaces, web services and simple adjustment mechanisms was required. A reliable interface to the software distribution system used to install required client applications was also very important in the selection process.
What functions the new solution had to offer in the areas of incident management, asset management, contract management and change management was clearly defined at WALDNER from the start. It was particularly important that the system maps the relevant functional areas fully integrated, allows comprehensive reporting and already offers the desired functions in the standard, so that it can be used "out-of-the-box".
Solution competence and usability were the deciding factors
Subsequently, leading solution providers were researched, checked for their suitability and finally invited to system presentations on site.
"In the process simulations of our 'hands-on test', in the context of which we compared both the range of functions as well as the usability and the approach, the chaff separated from the wheat. It quickly became clear that mIT solutions GmbH, with its very distinctive solution and process expertise and EcholoN, was able to best meet our complex requirements”, explains Thilo Rauch.
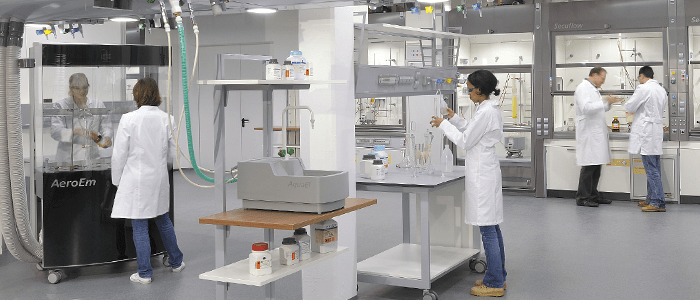
In addition to industrial plants, WALDNER also manufactures modern laboratory and training facilities.
In the course of the system introduction, a continuous improvement process was also initiated at the process level, whereby individual processes, such as the employees create a Service Level Agreement (SLA) or assign licenses, have been reorganized. This is intended to successively simplify both the electronic data acquisition in the system and the commercial administration of the assets. While faults in maintenance used to be reported and processed either by e-mail, in Excel, paper-based or even verbally, today the incidents are recorded in a very structured manner via the EcholoN platform and can be logged in a comprehensible manner.
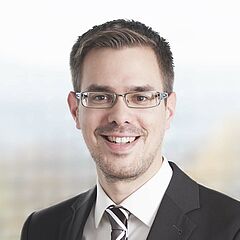
"This enables us to see at any time and on an ad-hoc basis what the situation in the respective service areas or in relation to individual assets is with regard to the amount of disruptions and our resource utilization. All employees are also on the same level of information and can provide information about the current ticket status at any time. In addition, we had to do a lot of work with our systems at the time to set up reliable reminder functions for regular maintenance intervals and test cycles. In EcholoN, on the other hand, such workflows can be implemented very easily and comfortably, which ultimately benefits the service quality”, explains Thilo Rauch.
The service quality also benefits from the steadily growing knowledge database, since every incident and every problem solution is documented in detail and possible solution scenarios are provided for a wide variety of malfunctions.
"Today, with EcholoN, we can create a complete documentation for our suppliers at the push of a button, how often the hydraulic cylinder of the lifting device was broken, which test mechanisms were implemented and whether there were any abnormalities at the regular maintenance intervals. All information about an asset, such as Linked contracts, details on suppliers, manufacturers and service providers as well as the machine history can now be called up directly in the central service management system without long searches. This enables us to better assess the service quality - internally and externally - according to individual areas and to better align resource management with actual needs. ”
Today the new service management solution is used at WALDNER at 40 service workplaces. In the next stage of expansion, the service and maintenance staff are to be equipped with mobile devices to: to support the diagnostic / test programs and routine maintenance with the help of standardized checklists. It is planned to extend EcholoN use to other service areas such as external customer service and all subsidiaries of the WALDNER group of companies in the medium and long term.