McDonald's and Service Integrator REPA - GEV rely on EcholoN for effective canteen kitchen service
Efficient service and fast spare parts supply in canteen kitchen technology
Reliable and fast service in canteen kitchen technology is of cardinal importance for maintaining the smooth business operations of McDonald's restaurants and for the quality management of the products. In 2012, the world's leading system gastronomy, together with GEV, exclusive service partner for McDonald's commercial kitchen technology and responsible for the central control of spare parts supply, implemented a new, pioneering service concept for over 1,400 restaurant businesses across Germany, based on the Service Management Suite EcholoN from the Hamburg-based mIT solutions GmbH.
GEV Großküchen-Ersatzteil-Vertrieb GmbH is Europe's leading dealer for spare parts in the commercial kitchen and supplies over 7,500 specialist dealers, repair service providers and industrial companies in Germany alone. To this end, the REPA - GEV constantly has over 85,000 items for devices and accessories from 700 manufacturers in stock.
Thanks to state-of-the-art logistics and an efficient service organization, the company guarantees extremely short delivery times for required spare parts within just 24 hours.
The supply of spare parts at all times and effective service are critical factors for commercial kitchens today, which ultimately also prompted McDonald's Germany 2011 to completely reorganize the previous after-sales service concept.
As a competent service integrator and reliable exclusive partner for commercial kitchen technology alongside McDonald's, REPA - GEV has since supported the restructuring and optimization of service and spare parts processes in around 1,440 restaurant branches across Germany.
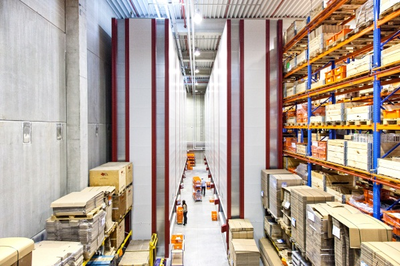
GEV is Europe's leading dealer for spare parts in canteen kitchens and restaurants
In the course of the service reorganization, McDonald's first defined specific IT requirements, et al with regard to data storage, the automation of service processes, reliable cost analyzes and electronic accounting. This should create the basis for successful and above all long-term effective cooperation. Since the previously used service management software at REPA - GEV could only partially depict the complex requirements, the decision ultimately grew to replace the old system with a new, powerful and needs-based service system.
.
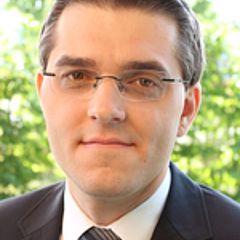
"To date, we have used the service module of our ERP system to map our service processes. With this addon, however, it was only possible to a very limited extent to automate service processes, to place orders with external service providers or to exchange order-related data with the respective service company electronically. In addition, there was simply a lack of functional depth in order to handle the service processes consistently, quickly and efficiently in accordance with the defined requirements. It was therefore hardly possible or only with disproportionate effort to meet the required service level agreements and availability times for spare parts", summarizes Matthias Göttler, responsible project and service manager at GEV.
Process orientation was decisive
In the subsequent selection process initiated by REPA - GEV and McDonald's, the market was first explored for suitable service management solutions. In the course of the project tender, potential suppliers were contacted and their solutions were put through their paces in terms of the specific requirements of REPA - GEV and McDonald's.
After a short time, the choice fell on Service Management EcholoN and mIT solutions GmbH, who convinced the project team with their solution competence, process orientation and flexibility of the solution: "At this point, it was easy to see that EcholoN has a certain degree of functional and technical maturity compared to the other service solutions and that it can cope with even the most complex service requirements. For our service employees, the software is not only very user-friendly and easy to understand, but also has a high level of adaptability, so that completely new service processes can be mapped in the system", explains Matthias Göttler. "But the underlying EcholoN license model, which is optimally suited to our purpose and the organizational constellation, also contributed to our decision."
The decision to introduce EcholoN was made in January 2012, the project kickoff followed in February and the new solution, which has been used by around 150 users since then, went live for the first time in May 2012.
"The time frame available from just three months to the start of productive operation required tight time management and optimal interaction between all those involved," said Göttler. In this tight time frame, not only the technical implementation, the connection to the REPA - GEV ERP system and the training of the employees were carried out, but also the reorganization of individual areas and processes.
With the introduction of the new solution, the communication and accounting processes at McDonald's changed. As a result, service calls are no longer carried out directly between McDonald's and the responsible service company. The commissioning of service assignments and control of the service technicians is carried out today by the REPA - GEV as the central service hub.
In addition, individual service areas such as the ticket system with escalation management were redesigned and optimized, while, for example, incident management, data collection, reporting of service processes, invoice verification, electronic invoicing, warranty processing and commissioning documentation were redesigned.
The result was a completely new service concept at McDonald's, the REPA - GEV and the service providers involved in the process, which could be easily and reliably mapped with EcholoN despite the heterogeneous organizational structures.
Consistent service processes, even with external service providers
Setting up interlocking collaboration workflows was still completely unthinkable with the service module at that time. With the central service platform EcholoN, McDonald's Restaurants, REPA - GEV and the respective service providers in the restaurant chain now have functional and, above all, efficient service processes that significantly facilitate collaboration and guarantee the highest service levels.
“This not only offers very short, effective information channels, but also ensures optimal networking of all partners in the complex collaboration network. This means that we can not only reliably comply with McDonald's restrictive guidelines and requirements with regard to response and service delivery times, but also save process costs in the control of service processes ”,
praises REPA - GEV managing director Alexander Wiegand. If a technical malfunction occurs in one of the restaurants, the McDonald's operators contact the REPA - GEV service team available around the clock via a free hotline.
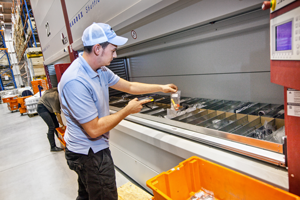
High-bay warehouse and direct spare parts supply for all McDonald's service technicians in order picking.
The REPA - GEV service employees are helpdesk technicians certified by the respective canteen kitchen manufacturers, who already offer reliable and competent support in the 1st level with preconfigured checklists in EcholoN, a multidimensional knowledge database and integrated exploded drawings and operating instructions.
If telephone support is still not able to remedy the fault, an order can be generated directly via EcholoN to the assigned service company. The relevant malfunction details including the possible error identification, article numbers and order information are then forwarded directly electronically. The responsible service company then uses the EcholoN system to order its field service technician to the restaurant and handles the order independently.
Digitization of work reports on mobile devices
While the service technician used to create his service report in paper form after the fault had been rectified and had it countersigned by the restaurant manager, data collection for the subsequent accounting process can now be done completely electronically in EcholoN with mobile devices and without redundancies. The system then automatically generates the invoice for the order at REPA - GEV.
This not only results in significantly shorter processing times, but also improves the evaluation and optimization of the service processes with every digitized work report. After the accounting processes at the first 70 restaurant businesses were successfully converted, the nationwide roll-out and the connection of further restaurants and service providers followed in the second half of 2014.
While the service processes previously offered little transparency, today all processes are traceable, measurable and are centrally documented. "By working with EcholoN and the easy traceability of response times of the service companies, we can now implement appropriate measures to reduce the average response times and thus the downtime of the devices in the individual branches," said Alexander Wiegand.
In the next step, the comprehensive reporting options of the solution are to be used to a greater extent in order to illuminate the service processes flexibly and from different perspectives and to gain further insights into the optimization of relevant service indicators. As part of this, mIT solutions is also currently working on an information cockpit in order to provide the respective McDonald's franchisees with comprehensive service evaluations and management indicators.
For example, the owner can see at the touch of a button which device is causing which costs. Behind this is a constantly growing database and a 360° analysis platform from EcholoN for the most diverse perspectives (owner, service provider, REPA - GEV) and dimensions. On the other hand, the REPA - GEV employees can see which technician needs how long to repair which machine, which equipment training he has or which he actually operates in the event of a malfunction.
The successively growing service database of EcholoN thus provides REPA - GEV with an optimal basis for internal quality management and optimisation of resource control. An integrated, consistent workflow system subsequently offers the possibility of directly implementing targeted measures.